Manufacturing startup Desktop Metal gets $115 million to deliver metal 3D printing
by July 24, 2017 2:49 pm 290 views
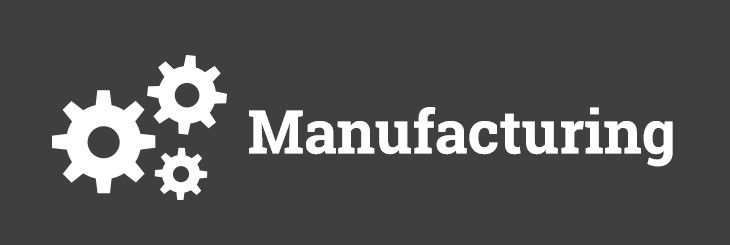
In what is sure to have long-range implications for global manufacturing, Desktop Metal — a Massachusetts company seeking to make metal 3D printing accessible to manufacturers and engineers — has announced the completion of a $115 million Series D investment round to further accelerate the company’s rapid business growth and adoption of end-to-end metal 3D printing systems.
Since its inception in October 2015, Desktop Metal has raised a total of $212 million in financing, with the Series D marking the largest individual private round for a metal additive manufacturing company.
The Series D round included “significant” new investment, the company stated, from New Enterprise Associates (NEA), GV (formerly Google Ventures), GE Ventures, Future Fund and Techtronic Industries (TTI), a leader in quality consumer, professional and industrial products, including Milwaukee Tool, AEG, Ryobi, Hoover, Oreck, VAX and Dirt Devil. Additional investors included Lowe’s, Lux Capital, Vertex Ventures, Moonrise Venture Partners, DCVC Opportunity, Tyche, Kleiner Perkins Caufield & Byers, Shenzhen Capital Group (SCGC) and Saudi Aramco.
According to Ric Fulop, CEO and co-founder of Desktop Metal, the funding will help fuel the company’s speed to market, expand its sales programs, as well as progress the development of advanced R&D. The company is also exploring international expansion as early as 2018.
“We are on the brink of an exciting transformation in how metal parts will be designed, prototyped, and ultimately mass produced,” Fulop said in a statement. “This latest funding puts us in an ideal position to ship our Studio System in the coming months and our Production System in 2018, while also enabling us to grow our company globally. The continued support of our investors underscores the power of our metal 3D printing solutions to help engineers and manufacturers, for the first time, apply metal 3D printing for the entire product development lifecycle – from prototyping to cost effectively mass producing complex metal parts.”
The funding announcement comes within three months of Desktop Metal launching two metal 3D printing systems covering the full product lifecycle — from prototyping to mass production. The Studio System is the first office-friendly metal 3D printing system for rapid prototyping and is 10 times less expensive than existing technology today. To manufacture metal 3D printed parts at scale, Desktop Metal also debuted the only 3D printing system for mass production of high resolution metal parts today, the Production System. Using new, proprietary Single Pass Jetting (SPJ) technology, the Production System is 100 times faster than today’s laser-based additive manufacturing systems.
“Our mission at GE Ventures is to invest in startups with cutting-edge technologies,” said Steve Taub, senior director of advanced manufacturing, GE Ventures. “Desktop Metal’s team and technology have delivered on exactly what they’ve promised: a vision to change the way parts are manufactured, with the innovative metal 3D printing technology to make that a reality. We see a huge potential for engineers to rethink the way parts and products are made both domestically and abroad.”
“We’re enthusiastic about supporting Desktop Metal,” said Scott Griswold, president of accessories at Milwaukee Tool, an industry leading manufacturer of professional, heavy-duty tools and accessories, and subsidiary of TTI. “Desktop Metal’s advances in metal 3D printing are disruptive by reducing product development time and by enabling 3D printed parts to be affordably brought to market.”
“We are blown away by the performance of the team and the technology at Desktop Metal, and that’s why we doubled down on our early investment in the company with our participation in this round,” said Dayna Grayson, Partner at NEA. “They have opened up a new frontier for 3D printing with the speed and quality they can attain, redefining the term ‘3D printing’ itself to mean much more than simply morphing a digital model into a physical model on a one-off basis. This could affect manufacturing and processes for decades to come.”