Food shippers struggle with labor issues, inflation and uncertainty
by November 3, 2022 1:38 pm 866 views
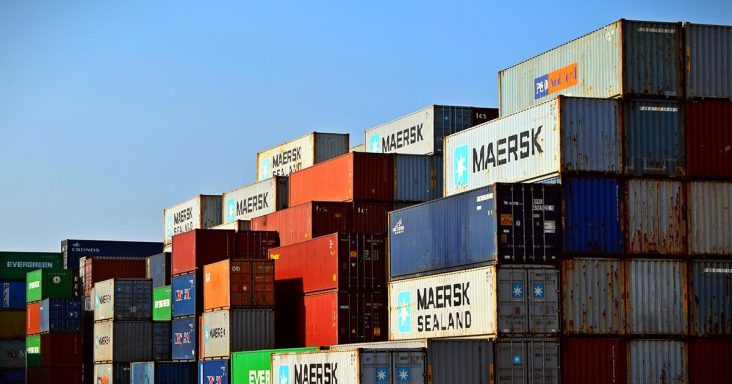
The most significant challenges the food shipping industry faces are labor and talent management, transportation capacity issues and supply and demand planning, according to recent survey results. Food shippers also are concerned about rising inflation and geopolitical uncertainty negatively impacting the fourth quarter.
Trade group Food Shippers of America and FourKites, a supply chain visibility platform provider, recently released a report on the results of a June survey regarding industry challenges, the financial impact of product shortages and e-commerce growth. The survey comprised 118 participants, including food manufacturers, retailers, distributors and third-party logistics companies and freight brokers.
More than three-quarters of respondents said they are concerned or very concerned that rising inflation and geopolitical uncertainty will negatively affect the fourth quarter. Still, 13.7% of respondents were neutral, and 9.6% were only somewhat concerned. Another 1.4% of respondents weren’t concerned at all.
According to the report, food shippers are taking steps to “future-proof” supply chains, and they include partner-driven relationships, outsourcing and continued technology investments.
Almost half of the respondents said their biggest challenge was labor and talent management, while 39.2% said transportation capacity issues were the top challenge. Supply and demand planning (35.4%), transportation rate issues (29.1%) and warehousing capacity issues (15.2%) rounded out the top issues.
The report shows that logistics visibility reduces stress and work on operations teams in the food chain by reducing customer service calls and manual processes. Visibility can improve planning and reduce inventory with real-time supplier data while lowering safety stock and improving forecasting accuracy.
Over the past three years, the impact of the COVID-19 pandemic on labor was the most serious disruption to the operations of food shippers, according to 55.7% of respondents. Other disruptions to the operations comprised over-the-road capacity (44.3%), port delays and congestion (30.4%) and changes in consumer behavior and buying patterns (21.5%).
Global food companies struggling with problems related to port delays and congestion could benefit from ocean exception management combined with ocean visibility to lower transportation costs, reduce demurrage and detention fees, improve customer satisfaction, improve product availability and generate less spoilage, the report shows. Visibility allows food shippers to improve vendor relations and performance by collaborating in real-time with suppliers and fulfillment teams, which will increase the ability to react to changes in buyer behavior and purchasing patterns.
According to the report, product shortages have had no financial impact on 43% of respondents’ businesses. However, 45.6% of respondents said the shortages have contributed to a less than 15% decline or miss in sales. Also, 10.1% of respondents attributed the shortages to a 15% to 30% decline or miss in sales.
Shippers increased inventories to minimize the shortages, but the build-up has increased costs. Food chain visibility allows shippers to integrate their transportation, supply and warehouse management systems with “order-level detail to ultimately break down silos and create new opportunities for supply chain optimization,” the report shows. “Supply chain integration allows you to have a significant impact on avoiding product shortages, or a decline or miss in sales.”
Over the next six months, most respondents expect a rise in e-commerce use and home delivery and last-mile services and store pick-up. The respondents attributed the increase to convenience. According to the U.S. Department of Commerce, e-commerce sales rose by 14.2% to $870.8 billion in 2021 from 2020. The sales were up 45% from 2019.
The challenges regarding last-mile delivery include cost, predictability, flexibility and customer satisfaction. As the number of deliveries rises, food shippers’ expenses will increase. According to Capgemini, last-mile delivery accounts for 41% of total supply chain costs. Real-time visibility can help shippers achieve better data, partner collaboration and network enablement, the report shows.
More than half of respondents said they’ve not noticed a decrease in customer loyalty since the start of the pandemic. However, 34.3% of respondents said they have seen a decrease. About 15% of respondents were unsure of such a decline. The report shows that supply chain visibility has enabled food shippers and their providers to reduce food chain costs and improve the customer experience, bolstering customer loyalty.
Respondents said the most significant initiatives to reduce labor costs have included an increased focus on recruiting and retention; automation of redundant tasks and technology applications; consolidating assignments; improving benefits, including higher pay and flexible hours; and more use of contract or outsourced labor. Labor is among the top expenses for grocers, including staffing stores and managing fulfillment and distribution centers.
“Because manual processes and siloed systems can lead to inefficiencies that drain budgets, food chain executives are increasingly turning to freight tracking and visibility software, as well as real-time transportation visibility platforms, to automate manual tasks and streamline collaboration – saving time and money across a variety of roles,” according to the report. The platforms provide live tracking and status updates on the location of food products and materials while in transit. This information is often collected through integration with GPS and telematics devices on the truck or shipping container and made available on a cloud-based platform.
According to FreightWaves, real-time visibility providers, including project44 and FourKites, were ranked among the top 25 most innovative and disruptive companies in the freight technology space. For the second consecutive year, project44 ranked No. 1 on FreightWaves’ FreightTech 25 list, while FourKites was No. 5 for the second year in a row. Lowell-based carrier J.B. Hunt Transport Services rose to No. 7, from No. 11 last year. Amazon Freight fell to No. 6, from No. 3. Amazon Freight was ranked No. 1 two years ago.