Meat market watchers note production, financial issues with COVID-19 outbreak
by April 30, 2020 3:40 pm 1,055 views
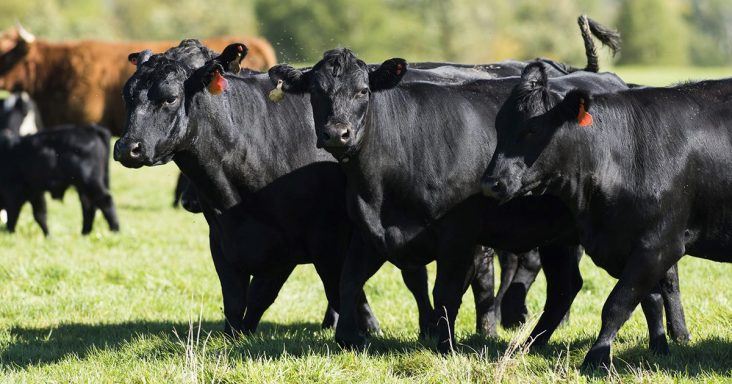
Derrell Peel, livestock marketing analyst at Oklahoma State University, has said a recent emergency order from President Donald Trump mandating meat processing plants remain open doesn’t change much for the meatpacking industry, outside of the liability protection for the companies.
“Meat packers and processors want to stay open and they are trying to do so,” Peel said. “Their challenge is having the necessary workforce to run the plants. The federal government can’t send in the National Guard to cut up meat. These plants are reliant on a healthy workforce. Without the workforce, you are not going to have much meat.”
Travis Justice, the chief economist for Arkansas Farm Bureau Federation, said processing plants were already trying to stay open because without them in operation, there is a kink in the food supply chain. He said the packing industry has operated on a just-in-time process, and now that worker absences have risen, line speeds have been slowed and there are fewer production runs. Fewer production runs decreased slaughter capacity causing cattle and hog supplies to build up at one end of the supply chain.
Justice said as COVID-19 outbreaks have occurred, companies like Tyson Foods and Cargill have worked with CDC and health officials to take added precautions, require testing and enforce quarantines among those with positive results. He said the emergency order is help for packers because it provides them some added support on operational guidelines and liability protection against lawsuits.
Justice and Peel said the biggest reason plants are running at reduced capacity is the lack of a workforce. Justice said when schools closed that was the first wave of absences. When COVID-19 positive cases began to escalate, the health concerns were the second wave of absences.
PACKER, FEEDLOT CHALLENGES
Peel said slaughter for pork and beef were each down 40% this week. He said with more packing plants temporarily going offline for testing and cleaning, slaughter reduction will continue for several more weeks. The meatpacking industry downsized capacity over the past decade which made the beef packing industry regional. Peel said the Tyson plant in Pasco, Wash., serves the majority of cattle ranchers in the Northwest and when that plant reduces slaughter the cattlemen in that market have no one else to bid on their livestock.
“I recently spoke to a rancher in that area who said with the Pasco plant closed he has nowhere to market his cattle. The JBS Greeley, Colo., plant was also closed for two weeks, but it came back online at the time the Pasco plant closed. These are huge packers and they serve the Western half of the industry,” Peel said.
Peel said this week there were 300,000 head of cattle backed up in the U.S. supply chain. Peel expects that number will escalate to 500,000 head by June as plants continue to close for testing and then reopen and run at less than the optimum capacity for the foreseeable future.
“Even when the worst of the COVID-19 outbreak is over, plants will still have to abide by the social distancing guidelines and I don’t see them running at more 90% capacity after that. There will be added costs to production because of the extra cleaning protocol and slower line speeds. While cattle prices are low for packers, the cost of production has gone up significantly. They are paying workers who are not there, giving bonuses to keep workers on the job and running plants at suboptimal levels of capacity,” Peel said.
He said packer margins may look high but so is the cost of operation. The margin between revenue derived from the meat, hide and offal sales less the cost of the fed steer or heifer is running more than $700 per head slaughtered this week, but the cost of operation is also certainly greater for packers, Peel said.
Peel said as cattle back up in feedlots those operating costs also rise. Sterling Marketing said this week feedlots saw their average margin losses rise to $262 per head. The losses escalated from $24 in the past month as the situation persisted. Pork feedlots report losses of $50 per head this week and packer margins were $67 per head. John Nalivka of Sterling Marketing said feedlots are holding cattle that need to go slaughter but they don’t need to gain more weight or their price will be severely diminished.
Peel said the industry has a maintenance ration but never really put it into use. He said the feed ration consists of 60% forage and silage to allow for weights to remain optimal for slaughter. He said the industry is likely going to have to use this ration with some uncertainty of its effectiveness and impact on beef quality. Navika said the situation in farrow-to-finish hog production operations is much more dire as the system is built on throughput efficiencies.
“Finished market hogs are not the same situation as finished cattle. At the same time, feeder pigs are ready and need to be placed in the finishing barn – of which there is now no space. This situation goes well beyond feeding at higher cost of gain,” Peel said.
Justice said there are anecdotal stories of animals being euthanized and buried because no production facility could take them. He said most chicken plants in the south are operating albeit at some reduced capacity. Processors in the Northwest such as Perdue have had a harder time staying open. Justice said Iowa and the Midwest were hit hard and there will likely be some depopulation of hogs if plants can’t reopen soon. He said the cattle industry will limp along and it may take the rest of this year for cattle prices to start to rebound. That rebound will likely depend on how long the recession lasts.
Peel said the reduced production of pork and beef will likely continue indefinitely even when restaurants fully reopen. Restaurants and foodservice are about 50% of the meat industry sales. However, most hamburger meat is imported and will likely still be the case, Peel added.