Former Rolls-Royce North America executive highlights what Fort Smith, state must do to compete for advanced manufacturing jobs
by May 4, 2018 5:07 pm 1,988 views
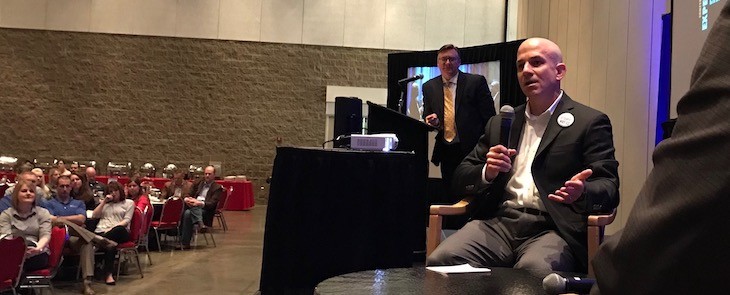
Jason Green, vice-president of human resources for ABB/Baldor, talks about workforce development during a panel discussion conducted by the Fort Smith Regional Chamber of Commerce and hosted by Talk Business & Politics.
Good-paying jobs are the “new currency” of the global economy, and one former industrialist believes Fort Smith is well-positioned to compete for them.
Tom Loehr, former executive vice-president of Rolls-Royce North America, shared “a peek behind the curtain” regarding what site selectors for companies like the one he used to help manage are looking for when it comes to opening new facilities. At the top of the list — a qualified workforce and workforce training initiatives. Loehr spoke during the First Friday Breakfast hosted by the Fort Smith Regional Chamber of Commerce.
Fort Smith, Loehr said, can compete successfully if it channels resources to the areas that are most important, adopting a focused pursuit mindset instead of one that is broader in scope. Just like an Olympian cannot go to the Olympics thinking he’ll win gold in every event, Loehr said, ”It’s also silly to think that a region can compete for every manufacturing job because manufacturing is very differentiated. It’s not a one-size-fits-all.”
Low-level jobs are “destined to be sourced in a developing country,” so Fort Smith should be like the “internal rotating parts of an engine,” which have “conditional integrity down to a micron, or smaller than the width of a human hair.”
“These operate at a high speed and high temperatures. In fact, a turbine blade operates in an environment that is 200 degrees above its melting point, and it does it by precise airflow that circulates around that blade and protects it. This requires a high level of skill. This is advanced manufacturing. This is ‘good-paying jobs.’ This needs to be sourced in a highly-developed nation. This is what we should be competing for, and this is what should form our thinking around priorities and investments,” Loehr said.
To emphasize the importance and need for advanced manufacturing jobs in the U.S. (and Fort Smith), Loehr said there is an anticipated 3.5 million jobs that will be open due to growth and retirement by 2025 along with 600,000 positions that are currently unfilled. Subtract advanced manufacturing’s “replenishment capacity” of 1.5 million jobs, and that leaves an expected shortfall of 2.6 million jobs in the next seven years. Furthermore, for each “direct manufacturing job,” Loehr said, four other ancillary jobs are currently supported. In the next few years, that same direct advanced manufacturing job will support 16.
WHAT INDUSTRIES ARE LOOKING FOR
When Loehr was at Rolls-Royce North America, he was integral to the decision-making process of where to build a facility, when to expand, and “when to let one close.” As an industrialist having to make decisions on $200 million factories, the quality of workforce training initiatives in the community were vital, Loehr said. Not investing in it as a community “puts off our youth and industrialists, and we’re not going to succeed in the global competition for advanced manufacturing jobs.”
“Students expect they will be educated in a system that creates a good-paying job, and that’s not an unreasonable expectation,” Loehr said, adding that industrialists, before making a decision, “know how many equivalent skill sets there are employed in a 60-mile radius. They know how many students are enrolled in applicable programs in community colleges. They know what the burn rate is. They know exactly what the price of elasticity is going to be when they move into that market. Don’t think there are facilities that don’t do their homework on this thing.”
Loehr said there is a major “symbiotic relationship” between economic development and education.
“The reason industrialists are so interested in education, is that skill of the workforce is their number one risk. When you look at the education system as a means of sustaining ourselves, education is critical to advanced manufacturers. Yes, we look at your standards of testing, your proficiencies in science and math and reading comprehension. It matters. It’s important.”
But on the other side of that, education has “a huge reliance on industry and economic development.” Loehr said these two elements bring education funding, and if a community is failing at economic development and attracting and retaining industries, then “year after year, educators are asked to do more with less. In fact, all manner of public services are asked to do more with less.”
PIPELINE AND EDUCATION
Communities that want to capitalize on these needs should have a strong workforce and a pipeline. In a panel discussion following Loehr’s keynote hosted by Talk Business & Politics, Jason Green, vice-president of human resources for ABB/Baldor, complimented the existing Fort Smith workforce but highlighted this need for a viable pipeline of future talent.
When it comes to workforce, Green said, “Fort Smith can compete with most regions and communities, but that workforce is employed. When you think about trying to attract employers to this region, you have to have a pipeline of talent to complement that existing workforce. I will brag on (the workforce) every single day, but where we can improve is building that pipeline for the future.”
James Reed, president and CEO of Van Buren-based carrier USA Truck, agreed, noting that “Everyone of my senior leadership team have been added from outside this community in the last 18 months. While we’re excited that we have been able to draw talent from Phoenix and Seattle and these big markets that we compete with, we also recognize it as a failure. We need to develop leadership and management capability here locally with the end goal at least at USA Truck of having 80% of future management or promotions coming from within.” That said, Reed noted he is “delightfully pleased with our frontline workers.”
Loehr acknowledged not being intimately familiar with Fort Smith’s workforce, but said it “looks a lot like a town where I grew up, a town where people were very proud of a day’s work.”
“They put themselves into it, and it’s one of the things that make a place like this competitive. But oh my God, let’s not waste that. Let’s equip our people with the right skills to compete in modern manufacturing and modern service provision. I challenge you to go on the internet and look at jobs like nondestructive testing and machining. There are pages and pages and pages of jobs.”
Loehr continued: “I think Fort Smith, Arkansas, can definitely compete, but let’s equip ourselves with the tools. We need a system where (high school students) can earn a two-year technical degree. They’re employed by an advanced manufacturer. That advanced manufacturer will fund a four-year degree.”
Loehr, referring to his own “Jimi Hendrix Experience” growing up in the 1970s, asked attendees to think of education not as a “Y-intersection” fork in the road, but as a “continuum of learning,” where students can earn skills, “hop off a little while and smell the roses,” then resume their training through intermittent periods in the labor force. “We have to have a system of education and learning and development that is flexible to who we are, the people that we are. And if they want to hop off and work for a few years and hop back on and earn that four-year degreee, great. Some of the best chief operating officers in America followed that path.”
Loehr pointed to Danville, Va. as an example of a town that suffered “significant loss” in its textile industry but was able to reinvent itself around advanced manufacturing and workforce training initiatives. Now a student there can “come out at 19 making $20 an hour. All the talking heads in the world won’t say as much as a 19-year-old driving a candy-apple red mustang.”