Subs See Costs Rise As Economy Slows
by September 11, 2006 12:00 am 109 views
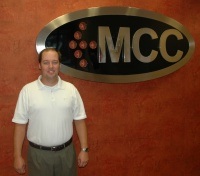
Skilled labor is in short supply and material costs are high but Northwest Arkansas keeps building.
Labor shortages and prices of energy and materials have been working against construction, taking the edge of the sharp market.
“We’re seeing a trend starting to taper off now,” said Mike Malone, president of Malone’s Mechanical in Van Buren. “It’s not as gung-ho as usual.”
National numbers confirm a decrease in construction confidence. On Aug. 23, the International Profit Associates Small Business Research Board released results of their study showing that contractors’ confidence in the economy fell 40 percent during the past three months.
But area subcontractors remain upbeat as the economy stabilizes.
“We’re still very positive about the short- and long-term of Northwest Arkansas,” said Hex Bisby, CFO of Multi-Craft Contractors Inc. in Springdale.
He said part of the slow down could be explained by the fiscal year winding down. Companies often delay starting new projects late in the year while they are more concerned with watching expenditures and meeting financial projections.
Malone offered another possible reason for the economic cool down. He said the industry especially becomes more tentative during election years as it watches for shifts in money channels. While presidential elections are worse, mid-term elections also affect decisions on construction of new facilities or expansions.
“They’ll put the project on hold to see how they shake out,” Malone said. “That’s been a pattern for many years.”
Even though the market may experience slower growth, many area subcontractors are saying the same thing — there’s not enough skilled labor.
Bisby said his company has been trying to overcome the problem with pay and benefits.
Multi-Craft also keeps good relationships with trade schools in the region in order to find employees. It also tries to lure future employees by offering apprentice programs, which in turn pay for schooling.
Malone also said apprenticeships are important. Getting new employees to work alongside journeymen gives his company a future pool of employees who could one day take over.
Malone said labor shortages limit what jobs you can handle, and is currently looking to increase its workforce. With the Fort Smith Sparks Regional Hospital and the upcoming Danville Hospital project, Malone wants to see an increase from 55 employees to about 80.
Getting skilled laborers is getting more costly though. Skilled workers hold most of the cards in a market where they are in short supply.
“We are paying more for those skilled workers to the point where their earnings are comparable to entry-level, white-collar jobs,” Bisby said.
When labor costs increase, so does the cost for the job. But the rising cost of materials is also causing problems.
“It’s hard to do a budget right now for our customers,” said Brent Tumey of Managed Subcontractors International in Rogers. “Six months from now it could be double what it costs now.”
To counter increasing materials costs, MSI purchases materials for projects ahead of time and will store them until they are needed. Tumey said his construction of the Courtyard by Marriot in Fort Smith is a prime example. From the time MSI ordered materials to when it was time to hang the dry wall, the cost increased 10 cents per SF.
By preparing for tomorrow, MSI knows the costs upfront. Tumey doesn’t have to later approach the contractor and tell him that his costs have increased.
“We have to make general contractors look good,” he said.