Phillips Corp. shows off robots at grand re-opening
by September 16, 2024 9:00 am 323 views
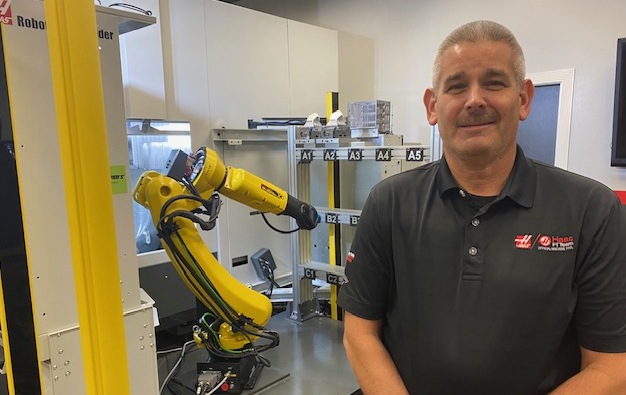
Michael Garner, President of Phillips Commercial Corp.
Humans and machines were both in motion at the Phillips Corporation showroom in Little Rock Sept. 12-13.
The showroom hosted a two-day Haas Automation “Don’t Fear Automation” Demo Days event where it demonstrated its industrial robotics and other products to customers, economic development officials, educators and others.
California-based Haas is the largest American machine tool builder and one of the world’s largest builders of CNC (computer numerical control) equipment.
Phillips Corporation is its factory outlet distributor for a 12-state territory that stretches from Arkansas to the Carolinas, New Jersey and Florida. It employs roughly 185 workers in total and 15 in Arkansas and has been in Little Rock more than 25 years. Its Arkansas employees work in sales and service positions. The company also sells industrial products made by other manufacturers.
President Michael Garner, who is based at the company’s Little Rock showroom, said customers include Dassault Falcon Jet and other aviation manufacturers, East Camden-based defense manufacturers Aerojet Rocketdyne and General Dynamics, Remington, and Fort Smith industrial motors manufacturer ABB. The U.S. Steel and Nucor steel plants in Mississippi County use Phillips equipment to lab test their products’ tensile strength.
A variety of machines were operating at the Demo Day event. One had made Lego-like blocks out of aluminum. Another had made sprockets from a chunk of circular steel. Some equipment is “subtractive” in that it cuts away raw material to make a product. Others are “additive” in that the robot assembles the product layer by layer. In some, the raw material moves while the robot largely remains in place. In others, it’s the robot that does most of the moving. Collaborative robots not surrounded by a cage or fence are designed to work alongside humans. Phillips offers 3-D printing products where a customer can produce whatever part it needs from a digital file.
“These robots are not to replace people,” said Garner, a 26-year company veteran. “They’re to enhance productivity. Most of our customers say, ‘We could add more equipment if we could find people to run it.’”
The two-day event included a Little Rock Regional Chamber of Commerce ribbon cutting Sept. 12 to celebrate the showroom’s recent expansion and remodeling. Secretary of Commerce Hugh McDonald, Arkansas State Chamber of Commerce President and CEO Randy Zook, and Little Rock Chamber President and CEO Jay Chesshir visited that day.
Also coming that day were roughly 60 educators, administrators, students and parents who traveled from as far away as Fort Smith, Jonesboro, Magnolia and Mena.
A number of Arkansas high school programs, including the Peak Innovation Center in Fort Smith and the Northeast Arkansas Career and Technical Center in Jonesboro, are “HTECs” or Haas Technical Educational Centers, that use Haas equipment in their advanced manufacturing programs. The company is also working with post-secondary institutions such as the University of Arkansas – Pulaski Technical College.
Garner is a founding board member of Be Pro Be Proud, an initiative of the Arkansas State Chamber of Commerce that, among other activities, introduces young people to skilled trade opportunities using tractor-trailers featuring interactive displays. Phillips has donated equipment for the Be Pro Be Proud programs in Arkansas and other states.
Garner said parents and grandparents tend to dissuade young people from manufacturing because they see it as dirty, dangerous work. But, he said, the Phillips showroom is typical of many of today’s facilities – climate-controlled, clean, and high-tech. A relatively small amount of training can lead to a substantial salary and a good career.
“Those jobs start out at $50,000 a year, and within 18 months we can have them making $65,000, and those jobs top out at about 100 grand a year,” he said. “We can’t find enough qualified people. We don’t care if they’ve got a four-year degree. All we care about is, do they know a little bit about our equipment? Can they navigate the control? Do they kind of know how to use the equipment, understand the processes? And then we will train them for the electrical and mechanical service side of things.”
Garner said today’s young people are well-suited to advanced manufacturing work.
“I can walk them over to that robot control, looks like an iPad, and in 15 minutes I can take a middle school student and teach him how to program a robot,” he said. “And they adapt to it. It’s intuitive to them because that’s how everything they’ve learned is that way.”