Business and Industry Training works to close the skilled trades gap
by October 31, 2022 1:41 pm 949 views
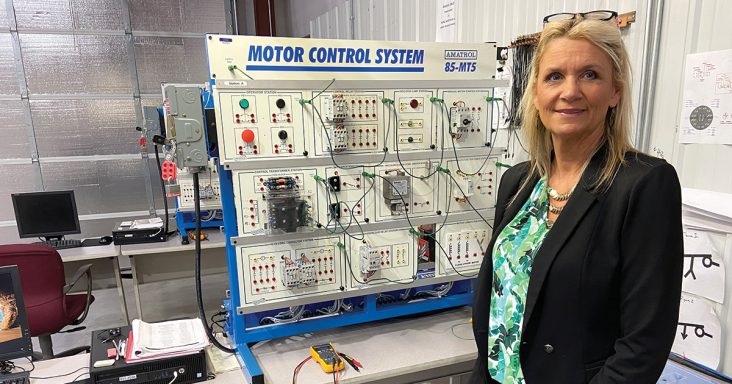
Julie McAllaster is director of Springdale-based Business and Industry Training. The nonprofit, with two locations in Northwest Arkansas, has provided skills training to area workers since 1996.
Springdale-based nonprofit Business and Industry Training (BIT) has provided flexible, self-paced skills training in Northwest Arkansas for the past 26 years. Recently, the organization expanded its capacity and reach through scholarships and support from area companies and foundations.
BIT director Julie McAllaster said it was founded when area plants faced a shortage of skilled labor, including electricians and plumbers, because they were retiring. Amid a push to pursue a college education, the plants needed workers more quickly than the time required to earn a degree. This led area business leaders to collaborate and establish the organization.
In 1996, the group created the Northwest Arkansas Industries for Education–doing business as Business and Industry Training–to provide workers with short-term, hands-on training outside of a classroom.
“It’s continuing to help industry needs of closing the skills gap and providing training for individuals,” McAllaster said.
She said that between 2020 and 2022, the number of training courses taken has risen between 65% and 70%, noting that the COVID-19 pandemic impacted training. The existing training capacity is about 60 people per day, not including when multiple people are at one training station. Office coordinator Sheri Nolan added that courses are full and have a waiting list.
In 2018, it opened a nearly 1,000-square-foot location at 201 S. Giles in Gentry to provide training for western Benton County workers. The following year, it relocated its Springdale site from Northwest Technical Institute to an almost 6,000-square-foot building at 1490 June Self Drive.
Over the past few months, the organization has received more than $230,000 in grants for training equipment and $45,000 in scholarships. Benton County gave $145,442 for the scholarships and new training equipment at the organization’s two locations. Arconic Foundation provided $45,000 for a new process control trainer.
McAllaster said a board of directors operates the organization, and more than half are employees of area companies. The organization’s staff work to ensure the training they offer remains relevant to companies’ needs by keeping in touch with them.
“We want to grow with the industry and not grow way too fast or not fast enough,” McAllaster said.
Jonathan King, a senior reliability engineer for Tyson Foods, has been BIT board president for the past six years. He explained the organization’s area impact and how it’s helped industry workers improve their skill sets.
“As a manager at a facility in Northwest Arkansas, we use them exclusively for assessments and training of our team members as well as skill advancements,” King said. “They do provide a service that we were not able to find anywhere else in regard to flexibility and short-term training that is very user specific in regard to their needs as well as their schedule.
“I think that part is significant because it’s not a standard, traditional semester-long program. You can go for a class anywhere from three to five weeks, depending on how much time commitment the individual can make. You can take a month off, two months off, and then pick up another course. It’s very flexible to your schedule, making it more successful.”
STUDENT FOCUS
Nolan said, initially, those trained were employees of area companies and people needing jobs. More recently, a greater focus has been on preparing high school students.
“Here’s another path where you can still make the same wages you would if you graduated college and got into a job there,” Nolan said. “You can get into this job … in a short period of time, with no student loans and get hired out of the gate … with benefits.”
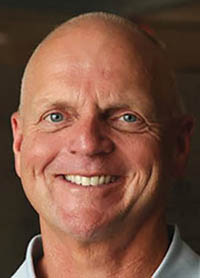
Rodney Ellis, workforce training director for Springdale Public Schools, said it chose BIT to offer career opportunities to students who didn’t have access to training programs during the day. He said the school district started to train students there while he worked in a similar role with Tyson Foods.
The most recent group of students completed training there last spring. Another group of students is expected to start soon, and he said a high school graduate who’s working continues to receive training there.
Soon, Ellis looks to have students receive robotics training there. Previously, students have received training in electronics, mechanical and fluid power. As students make progress, they’ll move into advanced electrical training, including motor controls, variable frequency drives and programmable logic controllers (PLCs).
TRAINING AREAS
The organization offers training in computer numerical control (CNC); mechanical drives; fluid power, comprising pneumatics, hydraulics, and robotics; electrical systems; motor controls; and PLCs. The latter consists of programming systems that make equipment run. McAllaster explained that the controllers used in food manufacturing could tell equipment when to add food to prepared meals based on each meal’s weight.
McAllaster said that key training areas include mechanical, electrical and PLCs, noting that automation is a new industry the organization is working to support. Soon, she expects to receive process control thermal training equipment, which is in the family of electrical and PLCs.
“We also do soft skills training,” McAllaster said. “We offer over 100 different classes. At Rockline, we trained their leads in the plant and sent an instructor there. We trained them twice a week, every other week. They picked the classes, and we went through the training with them.”
On- and off-site training is available to learn CPR, first aid, Excel, Occupational Safety and Health Administration (OSHA) standards, and confined spaces safety measures.
DEVELOPING RELATIONSHIPS
McAllaster and Nolan started at the organization in 2018 and have worked to develop relationships with clients.
“We know them, talk to them and find out, ‘Oh, somebody just had a baby, they just moved or had a family member pass away,’ Nolan said. “We find out why they aren’t at training.”
She said they find out to help them.
“I think that’s important because not many companies have that personal relationship with their customers,” she said. “I feel like we do a good job at that.”
Training is available at Springdale from 9 a.m. to 9 p.m., Monday to Thursday. It’s available at the Gentry location from 9 a.m. to 6 p.m., Monday to Thursday. Training is offered in three-hour segments daily. On average, students can complete each course in five to six weeks, McAllaster said.
The average cost per course is about $900, and McAllaster said payment plans are available. The organization also has scholarships, including a CNC scholarship valued at $2,000, based on the two courses required to complete the training.
Companies can receive grants to cover the training cost for their employees. The organization works with companies to receive grants from the Arkansas Office of Skills Development. The grants cover 75% of the training cost. Grants are available to cover 50% of the cost of soft skills training.
McAllaster said she would like to provide training at additional locations across the state as it’s needed. The organization has four full-time and four part-time staff.