The Supply Side: Walmart raises the bar on OTIF with suppliers
by April 2, 2019 12:41 pm 3,109 views
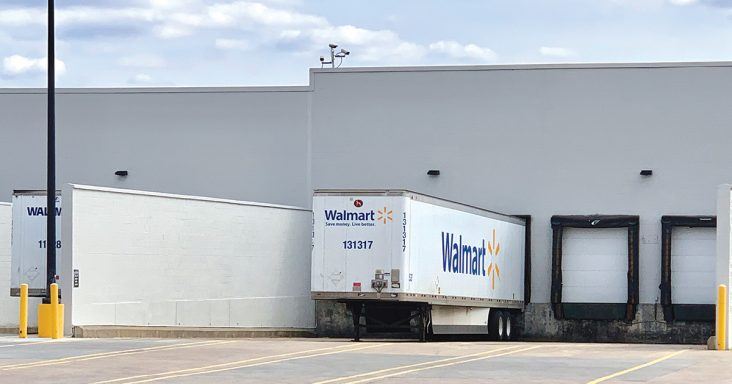
Walmart U.S. CEO Greg Foran recently said if the retail giant can’t get its orders on time from suppliers then nothing else it does works. Speaking to the investment community recently, Foran said two years ago the average on-time, in-full (OTIF) percentages were “horrifying.” He said they are better now, but more improvement is still needed.
Jason Shaffer, a senior director of digital operations for online grocery at Walmart, recently told suppliers the OTIF percentage for food and consumables was still a dismal 40% on average. That has prompted Walmart to step up its requirements for suppliers effective in May. Walmart unveiled the new requirements recently at its Supplier Growth Summit.
The new OTIF guidelines call for in-full orders of 95% for general merchandise and health and wellness. The in-full rate will be 97.5% for food and consumables this fiscal year. The on-time requirement increased to 87% for full truckload and 70% for less-than-truckload orders on prepaid freight within a two-day window. It was previously 85% and 50%, respectively. For suppliers who allow Walmart to handle their freight on a collect basis, they will have a 95% requirement on cases keyed and ready on time, Walmart said.
Suppliers will be subject to a 3% fine on short orders. In-full performance will be measured by the cases it receives compared to the cases it ordered. In general merchandise, the criteria is a 95% fill rate. If an order for 20 cases of hammers is filled with 18 cases, the order is short of the 95% guideline. Walmart said the supplier would be fined on the 3% on the two cases it was short. In the food and consumable categories that are faster-moving items, the threshold is higher at 97.5% fill rates. If Walmart ordered 20 cases of cereal and 19 cases were received, that constitutes a 95% fill rate. The supplier would be charged 3% for the one case the order was short.
Walmart has said OTIF and quality improvements have been positive since 2017, when it first implemented the OTIF rules. Last year, Walmart raised the ante again, increasing the OTIF threshold of full truckload orders to 85% with a two-day window.
Monique Picou, senior vice president of U.S flow at Walmart, recently told suppliers OTIF would continue to be a big focus for Walmart as low on-time, in-full metrics were still responsible for 30% of the product outages in stores.
Picou, who came to Walmart last summer, outlined the company’s flow priorities for her team. She said they include integrated planning and execution at a high level, while also delivering exceptional quality with speed and most importantly responding through agile service while also driving more sales. Picou replaced Kathryn McLay, who was promoted to executive vice president of Neighborhood Markets in August. Picou spent nearly 14 years at Procter & Gamble, where she held a number of positions including oversight of the global supply chain for Gillette.
She said Walmart will be deploying some new programs this year aimed at improving the cross-docking backlogs that exist for a number of small suppliers relying on the retailer’s own logistics services. Picou said Walmart will be using automated inbound scheduling that is being extended into the grocery network. Advance shipment notifications are also available with new electronic bills of lading, a required document to move a freight shipment. In July, Walmart will open the new automated consolidation center in Colton, Calif., designed to increase the efficiency of the LTL orders.
Walmart has admitted in recent years the consolidation centers it uses were part of the problem with the order backlog. The new consolidation center in Colton is a big investment Walmart is making to improve the efficiency of bundling smaller orders together in full truckloads, which are cheaper to haul. Walmart found plenty of inefficiencies in the 11 third-party consolidation centers the company uses, known as CenterPoint. The new center is an attempt to help suppliers using consolidation hit the stricter guidelines and keep shelves fully stocked at its 4,700 stores.
When the new center is open this summer, more automation will take place, allowing for better transparency up the supply chain. Walmart said the new system enables suppliers to fill one massive order instead of the 42 separate orders now required with the manual system. The new software will automatically scan and count the product as it arrives at the consolidation center. That information will be documented into Walmart’s systems so the retailer can react faster to replenishment issues.
Picou told suppliers the OTIF guidelines are working to increase what were dismally low numbers. Since 2017, she said OTIF has improved by 3,000 basis points, or 30%, and more focus is needed to continue the improvement that is aimed at ensuring products get to Walmart’s shelves on time.
Walmart said it does plan to offer more education classes via the Supplier Academy on Retail Link beginning in March to help suppliers get up to speed on the new protocol. Walmart said the revised OTIF protocol will launch in May, and the company is also making enhancements to its OTIF dashboard ahead of the higher guidelines.
Walmart urges suppliers to use the tools it has provided for free on its Supplier Academy web portal on Retail Link. Some of the resources include an expectation letter to suppliers that outlines the new program guidelines, interactive training videos on topics like order forecasting, out-of-stock root cause and OTIF updates for 2019. The site also provides tools and resources for suppliers on fill-rate improvement.
Editor’s note: The Supply Side section of Talk Business & Politics focuses on the companies, organizations, issues and individuals engaged in providing products and services to retailers. The Supply Side is managed by Talk Business & Politics and sponsored by Propak Logistics.