Fayetteville startup Little Bird Systems engineers feed inventory management system for poultry industry
by January 22, 2019 4:01 pm 1,826 views
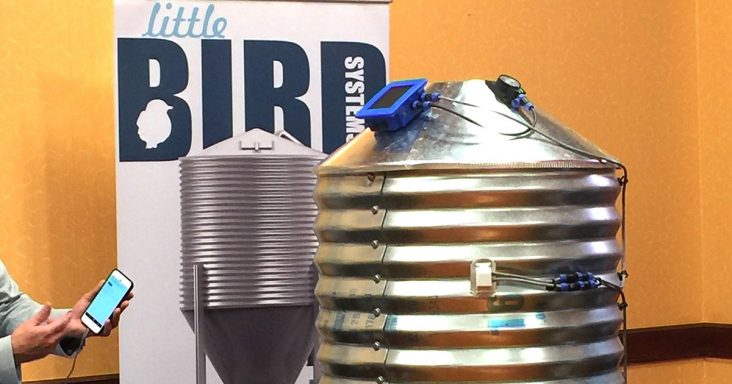
The Little Bird system was on display at the Northwest Arkansas Tech Council in late October. The feed inventory management system uses solar powered sensor technology and machine learning to detect the levels of feed inside a grain bin on poultry farms. That data is sent to the cloud and comes back in a report accessible via a smart phone application. The Fayetteville startup has been testing the system with local poultry companies for the past several months.
Fayetteville-based Little Bird Systems has taken on an industry challenge the poultry sector has faced for more than two decades.
Electrical engineers Byron Western and Edgar Cilio put their heads together in 2012 looking for an application to help poultry companies like Tyson Foods and Simmons Foods do a better job managing their feed inventory once it’s delivered out to grower farms.
Western, the CEO of Little Bird, said he was taking a master’s entrepreneur class taught by Dr. Carol Reeves at the University of Arkansas when he had the idea to use sensor technology and machine learning to help address the problem. Cilio, a co-founder who’s now chief technology officer, worked with Western on the project as a side gig at the time.
Western said they met with Jeff Amerine and Fayetteville consulting firm Startup Junkie and officials with the University of Arkansas Department of Agriculture, who all played a role in helping identify the right application and then gaining access to the test the technology as a solution.
The engineering duo then connected Jim Lewis, who now serves as the Little Bird’s chief operating officer. Lewis has experience in sales support to Walmart for companies such as IBM and Hewlett Packard, in addition to having some startup experience. He joined the team in 2012.
Western said poultry companies had no easy way to measure the feed inside the grain bins on their grower farms. Feed is the largest expense of growing a bird, comprising up to 60% of the total cost. It’s also expensive to operate the large trucks and deploy them to farms multiple times during a growing cycle if the grower is running low on feed.
The Little Bird team used the idea of how a glass of wine sings when a finger is pressed around the glass rim. The sound of the vibration varies with respect to how much liquid is in the glass. The fuller the glass is, the lower the pitch of the vibrations.
Western said he and Cilio figured out how to apply that vibration theory to a feed bin. They designed a patent-pending system of sensors that attach to the metal bins by magnets and a small mechanism that initiated the vibrations at various times during the growing cycle. The sensors capture the data vibrations and transfer that information to the cloud. Little Bird applies machine learning to the data to come up with a feed level reading that can be accessed with growers and poultry companies through a mobile phone app. The entire Little Bird system is powered by a small solar panel that is also attached by magnets to the top of the feed bin. Western said the solar pack has a long-life battery backup so the system is always available.
Lewis said the new system also gives poultry companies a better way to more accurately forecast the amount of feed individual farms will need. Little Bird did a case study test with one grower farm of small birds. The farm was located off the beaten path and had limited cell phone reception.
“This farm was kind of a worst-case scenario for us to start with,” Western said. “The poultry firm said the farm typically ran out of feed three to four times per flock. The feed truck had to make its way to that farm almost once a week. At the end of the flock cycle, the poultry company also reclaims any leftover feed in the bin. The average reclaim on this farm was 50,000 pounds, which was twice of the company’s 25,000 target.”
Little Bird installed its system on the test farm and began capturing vibration data. During the first flock, there was no outage of feed and the reclaimed feed was at the target 25,000 pounds. During the next flock, the system was used at the farm and there were no outages and the reclaimed feed was 15,000 pounds, well below the target.
“Every time a poultry integrator has to go to the mill and fill up a feed truck and make the rounds to these farms it’s an expense,” Western said. “The reclaimed feed pick up is also an expense. Our system over time gets better at calculating the feed levels. The machine learning is intuitive and the accuracy rates improve as more data is collected. We believe our system will allow companies to deliver more accurate levels of feed and reduce transportation costs associated with reclaims.”
The company said it is working with a third-party distributor — Diversified Agriculture — who already has relationships with the poultry industry to help sign up additional farms through various poultry integrators. Western said the Little Bird system costs roughly 50% less than the alternative large scales, which actually weigh the feed bins. He said the scale systems, which are also light sensitive, take four to five hours to install. Other competitors require drilling into the bins.
The Little Bird revenue model involves a setup cost and then data subscription and maintenance fees on a regular basis. Lewis said as more insights are gleaned over time, they will be shared with Little Bird subscribers in hopes of giving them a competitive advantage with respect to feed forecasting.
The Little Bird system was designed to be rugged and unobtrusive. The feed inside the bin is owned by the poultry company, but the bin itself is owned by the grower. Little Bird takes 20 minutes to install on the farm and requires no power other than solar. Western said because this system uses sensors linked to the cloud, it connects the farms. There are other applications the company is working on to help provide poultry companies more insights into the feed management systems.
“We have data to support a six-month return on investment and feel good about our position to market this product across the poultry industry,” Western said. “The poultry farms have lagged behind is applying sensor technology but our system hopes to change that and help poultry integrators keep better tabs on one of their biggest expenses — feed inventories.”
“This sounds like one of the many technology innovations being used in the food supply production today,” said Johnny Gunsaulis, staff chief of Benton County Extension Cooperative Service. “I can see where a system like this would be a benefit to farms and companies if the product is reliable enough to withstand the wind, snow, sleet and dust of the farm. It would also need to be able to account for the different ratio proportions that can impact feed density throughout the growing cycle.”
Gunsaulis said being able to better forecast feed inventory usage would be especially helpful during the winter when road conditions can sometimes make it difficult for big trucks to reach the farms.
Little Bird Systems has raised $1.1 million in working capital and is in the midst of another round for $400,000 this year. Western said the company has received funds from around the state, including the Arkansas Development Finance Authority seed and angel capital network. The company has scaled up from three to six people in the past couple of years as it looks for ways to transfer the technology to other applications.
Western said Little Bird’s passion is connecting businesses to the information within its environments, and bringing embedded wireless products for rreal-timemonitoring and data logging solutions.
He said Little Bird started with the poultry sector because the technology does solve a 25-year industry problem around better feed inventory monitoring. Industry leaders have been receptive to trying the technology.
Western said the company name refers to the saying about how information is shared — “a little bird told you.”