Walmart tests FAST unloader in 30 of its busiest supercenters
by June 6, 2018 6:23 pm 20,303 views
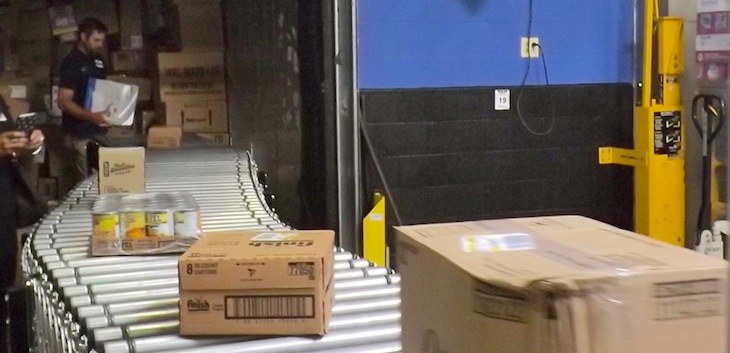
An employee at the Walmart Store No. 5260 in Rogers uses the FAST unloader.
The highest turnover among jobs in Walmart supercenters are with employees who unload trucks. The retailer hopes the use of an automated unloading conveyor system from Casi not only reduces employee turnover but also improves on-shelf product availability.
During the recent Walmart shareholders week, the media were provided a glimpse of the system at Walmart Store No. 5260 in Rogers. The system, now being tested in 30 stores, reduces the number of people needed to physically unload trucks and allows for product to reach the shelves faster, according to the retailer.
John Crecelius, vice president of central operations for Walmart U.S., told the media Walmart began testing the FAST unloader in a busy Plano Texas store about 18 months ago, and more units have been placed in some of the busiest stores, including the supercenter at Pleasant Grove Road in Rogers. He said Walmart has continued to tweak operations to perfect it for optimum efficiencies in the retail setting.
The conveyor system backs up to the truck bay and one employee places boxes from the truck onto the unit. The items are routed by department number to the proper area where a back room operator organizes the boxes on standing carts. When the cart is full, it’s sent out to the store and restocked to the shelves. The standing carts have ladders attached so employees can easily reach the highest shelves. Walmart said it rarely uses pallet jacks for routine stocking because the carts are more user-friendly. The retailer said the back room stockers are known as the CAP team – Customer Available Products.
The system from Frisco, Texas-based Casi also has the ability to sort items based on priority and department. Out-of-stocks are sorted by the machine for prioritization and because there are more workers designated out in the stores the CAP worker in the back can grab the out-of-stock cart and have it sent to the store more quickly for restocking. The system can sort 20.5 cases per minute.
Walmart declined to say how much the unit’s price but did say it’s proving to be worth the investment as turnover rates among unloaders have dramatically reduced. Rissa Pittman, manager at the Rogers store, said the FAST system reduced the number of unloaders from 8 to 4, which means more people can stock shelves rather than unload a truck. Walmart said back room CAP employees typically begin unloading a truck around 2 p.m. and it used to take 3.5 hours. Now it can be finished in 2 hours with the same average load of between 2,000 to 3,000 items.
When asked why it’s taking so long to roll units out to more stores, Crecelius said the retailer has more to learn about maintaining the equipment and scaling it. He said there are plans to rollout more this year, but not to all stores. Neighborhood Markets, for example, don’t have space in the back room for the large conveyor system. Also this unit is reserved for the busiest of stores which tend to be supercenters. He said the average stores can get up to 10 truck deliveries each week, but busy stores can do nearly twice that rate.
“We prepared ourselves for using this system about two years ago when we introduced Top Stock which moved most of the inventory out of the back room and onto the floor. We are also testing Bossanova, the roaming robot that tracks inventory on the shelves. You can imagine using both of these systems and the impact which can been on store in-stock levels,” he said.
Availability is another hindrance to using the unloader in more stores. Mark Ibbotson, executive vice president of central operations for Walmart U.S., said the retailer is adding the units as quickly as they can get them from the supplier. He said the retailer is also looking for other sources for unloaders because of the success it’s having on store efficiency and worker retention.
Walmart would not share specifics about improvements to on-shelf availability with the use of FAST unloader but did say it’s one of the systems to have the biggest impact overall on having items in stock. Creccelius said it also is the right thing to do because it’s easier on the workforce.
“There were many nights in our stores across the U.S. we couldn’t get the help needed to unload the trucks because the job is hard, but it’s one that’s very important to our success. This system has improved the quality of the unloader jobs and also allows us to have higher inventory in-stocks on fast-turning items,” Crecelius said.
He said Walmart’s distribution centers put a label on the boxes and there has not been any additional requirement from suppliers since Walmart has been using the FAST unloader. He said there has been little innovation in back room processes in the past 20 years.