FAA certifies GameBird aerobatic airplane to be built in Bentonville
by September 27, 2017 3:04 pm 6,212 views
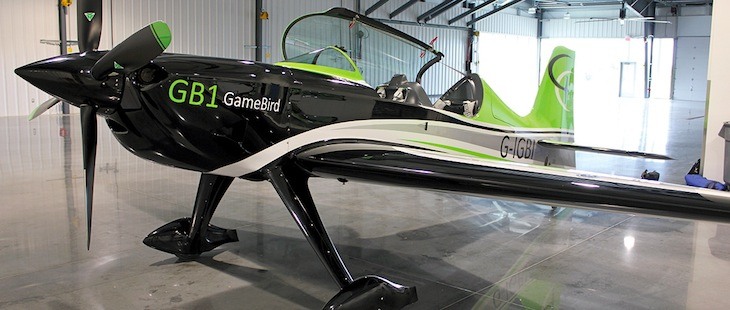
The GB1 GameBird recently received certification from the Federal Aviation Administration. Bentonville-based Game Composites will produce the aerobatic airplanes at its facility near Bentonville Municipal Airport.
A 10-minute discussion in the car five years ago led to the naming of an aerobatic airplane that recently received certification from the Federal Aviation Administration.
Aerobatic airplane designer Philipp Steinbach and business partner Steuart Walton, grandson of Wal-Mart Stores founder Sam Walton, were discussing a name for the project when they started listing off birds of prey, like eagle and hawk, but they didn’t sound fun, and more like something that would kill someone. Walton suggested game bird, and it sounded good to Steinbach before he knew game birds were bred to be shot.
“So far, nobody’s shot it down,” Steinbach joked.
Steinbach, who is from Germany, and Walton are partners in Game Composites, the manufacturer of the GB1 GameBird aerobatic airplane. On Aug. 29, Bentonville-based Game Composites received FAA certification for the GB1 GameBird. GB not only represents GameBird but also the famous “Gee Bee” racing planes in the 1930s. It’s also a homage to the company’s start in Great Britain. In 2016, the company relocated to a 40,000-square-foot building at Bentonville Municipal Airport.
“The U.S. is where the market is,” Steinbach said. He also chose Bentonville because it’s where his business partner lives. “It was an easy choice.”
Before the aerobatic airplane received FAA certification, it required design approval, airplane testing in flight and on the ground and compliance with the rules. Finally, the company needed to “convince the regulators you’ve done it all properly,” Steinbach said.
In April, the GameBird received certification from the European Aviation Safety Agency.
“American validation is just a validation through a bi-lateral agreement between EASA and the FAA,” he said. “We’ve done the design in Europe. The design authority is still in Europe. We just produce in the U.S. The European certification is validated by the FAA.”
Game Composites completed a parallel certification process with the federal and European agencies.
“Everything we sent to one regulator went to the other regulator at the same time,” Steinbach said. However, with two sets of regulators from different agencies completing the certification process, it didn’t save time for Game Composites. “The individual approval of each individual document took a bit longer,” he said.
The regulators had differing opinions, and it took them longer to agree.
ONE OF MOST REGULATED INDUSTRIES
Game Composites has started selling the GameBird, but the company didn’t have to wait for certification in order to sell the airplanes. However, companies that try to sell airplanes without FAA certification do so at great risk.
“So many people try to sell something that they couldn’t make or didn’t have or it turned out to be much more expensive. You shoot yourself in the knees by trying to sell too early,” Steinbach said. “Out of 100 aviation startups, less than five ever make it through certification. Most just die in the process.”
“It is a bit more complicated than a car,” he said. “And people look into this in much, much more detail than a car because you can kill people much easier. It’s probably the most regulated industry outside of the medical industry.”
The Game Composites team of four worked no less than 10 hours a day to achieve the certification in four years — a feat that often takes aircraft manufacturers 10 years to complete.
“We did all of the leg work required for certification first and not get hung up on the shiny bits,” he said. “The shiny bits are what people usually start with.” But the regulators aren’t interested what makes the airplane look good. “They’re worried about your safety, your reproducible quality, your quality management system and insurance rates.”
When asked what makes the airplane unique, Steinbach said the performance is better than the competition. He also said Game Composites is one of only four manufacturers of certified aerobatic airplanes in the world. One is in Minnesota and two are in Germany — one of which Steinbach founded and the other he worked for.
“Our production approval will be the first production approval of a new company in over 20 years in the U.S.,” Steinbach said. “It’s rather rare here.”
Steinbach said his favorite part of the GameBird is to fly it.
“If I could pick any airplane to have it would be this one,” he said. “It’s simply the best bang-for-the-buck airplane you can have.”
While the GameBird was built to be an aerobatic airplane, it can fly up to 300 mph and travel 1,000 nautical miles (about 1,150 miles). In May, Steinbach flew it to an airshow in Chino, Calif., traveling from Bentonville to Las Vegas, then from Las Vegas to Los Angeles. On Saturday, he went to the airshow; on Sunday, he flew to Phoenix; and from there, he flew nonstop to Bentonville.
FASTER THAN AIRLINES
“It does have legs,” Steinbach said.
He flew it from Northwest Arkansas to an airshow in Oshkosh, Wis., in less than three hours. One can travel to Dallas faster in the GameBird than any airliner, Steinbach explained. From here to McAllen International Airport “it’s seven hours with an airliner with getting touched and everything, and with the little airplane, it’s half the time and cheaper once you have it there and more fun.”
The frame of the GameBird is a carbon fiber composite structure, which makes it a lot lighter than traditional steel aerobatic airplanes. Each wing weighs 80 pounds, and empty, the airplane is 1,290 pounds, according to Flying magazine. It’s powered with a 303 horsepower, six cylinder engine and a four-blade prop. It has seating for two, with the pilot in the rear seat.
One model of the airplane will be available at a price of $400,000. So, far Game Composites has sold 11 of them. Each one will take 1,500 hours or about three months to build. Steinbach said the company has already started assembling parts for the aircraft, all of which will be built from the ground up at the Bentonville facility. Game Composites has 19 employees at that location but is expected to ramp up to 50 employees by the end of 2017.
“The whole group works on one airplane at a time, so one person will only make controls, the next person will only make wings, another guy will only do paint prep, another guy will do only spraying and supervision of paint prep, another guy will only put engines in and so forth,” he said. “Otherwise the training is too intense.”
Most of the activity at the Bentonville facility is where the workers are assembling parts for the airplane. They were making the parts by hand, and using a machine to impregnate the carbon fiber sheets. In another area is a large painting booth, but it’s yet to be used.
Steinbach said nothing needs to be painted as of yet, but when ready, the painting will require a significant part of the build. The remaining areas of the Bentonville facility include storage and a large hanger for the prototype.
The GameBird project started in 2013 in Great Britain, according to Flying magazine. Steinbach and his team used computer-aided design (CAD) software to create the airplane, and the airplane flew for the first time in July 2015. A year later, it made its first public appearance at the Flying Legends Airshow in England.