Long-time Walmart employee now ‘picking’ as a personal shopper
by July 18, 2024 10:39 am 2,228 views
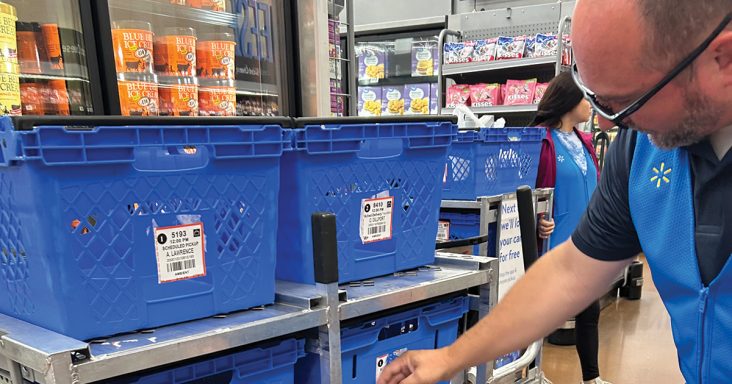
Walmart employee Lee Hiett works to fill online grocery orders.
It’s an early and busy shift for Lee Hiett, a 34-year Walmart employee, who shops almost nonstop for eight hours filling online grocery orders at the supercenter at 4208 Pleasant Crossing Blvd. in Rogers. Hiett, from Pea Ridge, has been with the personal shopper program since 2018.
By the end of 2024, Walmart is projected to have $18 billion more in online grocery sales than Amazon, giving the Bentonville-based retail giant 26.9% of the growing online grocery market, according to Compass Marketing. Online grocery is a major reason why Walmart’s comp sales continue to trend higher than other mass retailers.
Walmart would not have an online grocery business without personal shoppers like Hiett who transitioned from back-of-store operations to the personal shopper role in 2018 when the service was emerging.
“I know it sounds odd, but I like to shop. And it’s also rewarding to know this service helps busy families have time for other things. It’s also been fun to learn more about the products we carry,” Hiett said during a June 25 interview as he picked customer orders.
Hiett starts his eight-hour shift at 5 a.m., and said some employees start later in the day as the pickup service is available until 10 p.m. He’s one of about 100 employees who work in the pickup area of store No. 5260.
Store Manager Carlie Dodge said it’s one of the most sought-after jobs in the store by employees. At that store, personal shoppers comprise 20% of all store employees and represent one of the largest groups. She said demand continues to escalate for the service, which prompted investments in a larger space in the back-room area of the store with new freezers and chillers. More pickup parking spots were recently added and now sit at 27 bays. Walmart has said previously that store 5260 is one of the busiest for pickup in the region.
THE PROCESS
Walmart spent millions of dollars into its online grocery business to include the addition of artificial intelligence and robotics. But it’s the personal shoppers who make the service work at scale like in store 5260. Large machinery that initially sorted and stacked online orders in the Rogers supercenter has been removed, and there is a small army of people working behind swinging doors to get the online orders from Walmart’s system and set up totes for personal shoppers.
Some stagers take the carts from the personal shoppers, then separate the cold, chilled and ambient sacks and put them away until the customer is on the way to the store. Once the customer is on the way, the stager will pull together the entire order and have it ready when the customer arrives.
Hiett is the middle leg of that operation as a personal shopper. Outfitted with comfortable shoes, a water bottle, his blue vest and the Samsung phone Walmart provides, he checks out a cart from the back that tells him exactly how many items he will pick.
On June 25, he got a cart with five totes for five different customers and 35 items of shelf-stable foods to pick. He said if those customers had also ordered chilled or frozen foods, alcohol or general merchandise, the items would be picked by different employees. He said having multiple pickers who only work one area of the store is a more efficient use of time since those items are separated in the staging area.
When he checks out a cart in the backroom there is a label printout for each customer. The carts can hold up to eight totes. A label is affixed to each customer tote. After scanning a tote with his phone, the pick orders are loaded onto the device. Walmart’s algorithm builds a route for him to walk and provides a photo of the item and the aisle and section number.
SAFEGUARDS
On June 25, his pick started on aisle three for fire-roasted canned tomatoes. The phone showed a picture of the item to pick, he pointed the device at the shelf and the digital shelf label blinked showing him where it was. Hiett then picked up the item and scanned it into his phone to ensure it was the right product.
“If it’s not the right product, the phone won’t scan it, which is a safeguard against picking the wrong item,” Hiett said. ”Once I scan the item, then I bag it, but only if that’s what the customer has indicated they want. Some customers do not want plastic bags. Once the item is put into the tote, I scan the tote label and the next item for pickup is loaded into my phone.”
He said the 35 items on this pick trip included several of the same items for one customer. For instance, maybe they want three cans of corn, which makes for faster picking. He said some cart trips may have 100 items to pick, but that could be five six-packs of soda for one customer, or 12 cans of dog food for another.
Hiett said pickers keep bread and chips in separate bags. Chemicals like cleaning agents are put in separate bags and cannot be mixed with edibles. Raw meat also is bagged separately.
He was able to pick and bag 19 of the 35 items on his list in the first 15 minutes. One particular item he picked from the lighted shelf was not the right item and would not scan into the phone. It was out of place. He found the correct item behind it. Hiett said this happens sometimes, but the system won’t let pickers bag the wrong item.
It took Hiett about 30 minutes to pick the 35 items on his list, and he returned the cart to the back of the store to the staging area. He then grabbed another cart and tote labels and got back to work. Hiett said he logs between 20,000 and 25,000 steps a day when picking orders.
SUBSTITUTIONS
A big issue for customers is the substitution of an item that is out of stock. Hiett said Walmart takes this seriously. Using artificial intelligence, the system will suggest one or two possible substitutions. But there is not always a similar substitute. In that case, the picker has to choose another brand or an altogether different form of the item — for example, substituting frozen strawberries for fresh strawberries.
He said there is a team of pickers who only work on exceptions, and they offer a third level of quality control with substitutions. Customers are notified of the substitution and given the option to accept or decline before they get to the store. Again, at pickup, the employee will tell a customer about the substitution, and they can accept or decline.
“We work really hard to fill the entire order,” Hiett said. “But if we have to make a substitution, it will be as close as we can get to what the customer wants and at a comparable price. If a customer declines the substitution, then the system won’t likely offer that option again.”
Dodge said personal shoppers get training before they begin the position, then update training as changes are made in the store or the system. She said any scannable item is eligible for pickup as long as there are two or more of the items in stock.