A yarn too good to believe: 20-somethings create American textile company in Jonesboro
by March 4, 2021 11:21 am 106,189 views
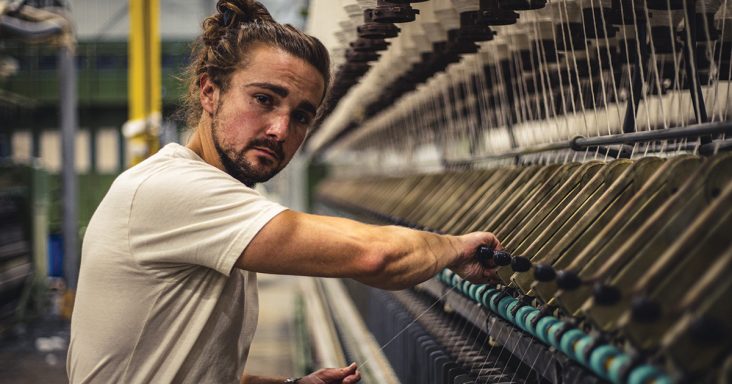
Harvest Produce Retail founder Paulie “Litt” Litowsky.
Paulie “Litt” Litowsky was chatting with a friend in New York City about high-end clothing and the quality of yarn required to make such garments. The friend told Litowsky, a former childhood actor and long-time producer, that no American-owned yarn company could compete with other garment producing countries such as China.
Litowsky, known for his roles in the movies “Speed Racer,” “Doubt,” “Jersey Girl,” and hit shows such as “Hope & Faith” and “Wizards of Waverly Place,” couldn’t believe what he was hearing.
Soon after, he contacted another college-age friend, Robert Rinearson, and the two decided to start their own high-end yarn producing company, Harvest Produce Retail (HPR).
Litowsky, 25 years old and no longer acting, told Talk Business & Politics it has taken more than two years to get HPR up and producing at its facility in the Craighead Technology and Industrial Park. Yarn production began at the same time as the pandemic started to grip the world in March 2020, but Litowsky and Rinearson both said the co-owners were undeterred.
“We didn’t just talk about it … we did it,” Litowsky said.
A New Jersey native, Litowsky had never been to Jonesboro before he found the building for his business. He visited Rinearson, 23, to discuss his business idea.
“He comes over to my house and says ‘I’ve got this great idea.’ At first, I thought he was crazy,” Rinearson said with a laugh.
Rinearson warmed to the idea, and Litowsky said he spent months reading as many books as he could about textiles. He soon realized that 97% of all clothing is produced overseas, but one key ingredient, cotton, is grown in the U.S.
The U.S. ranks third in terms of cotton production, producing about 4,336 metric tons each year. India (6,423 metric tons) and China (5,933 metric tons) rank first and second in the world. One bale of cotton, on average, will move around the world twice before it’s used to make clothing, he added.
Litowsky and Rinearson decided to locate their operations in the Mississippi Delta Region to stay close to the cotton they planned to turn into clothes. Memphis, Tenn., was a logical place for a yarn plant, but they couldn’t find a building to suit their needs, Litowsky said. During a Google search, he came across the city of Jonesboro, an hour away from downtown Memphis.
Once the duo had a building, they turned their attention to outfitting it with equipment and learning the trade. These turned into significant hurdles, Litowsky said.
The U.S. textile and garment industry produces about $70 billion per year as a sector, and it accounts for $13 billion each year in exports. But many of those products are made in other countries such as China, India and Brazil. Starting in the 1960s, wages in the textile industry rapidly decreased in the U.S. as other nations began to ramp up production. From 1994 to 2005, nearly 1 million textile-related jobs were lost in the U.S. China emerged as the leading textile and garment exporter in the world, exporting nearly $120 billion each year.
Litowsky said he knew he could never compete with China based on bulk production rates, but he believed they could create a higher quality product. Finding the right kind of training proved difficult, he said.
Eventually, they found a textile training program at Gaston College in North Carolina. Following a crash course, the two went about outfitting their factory with machines. Many were years old and had to be modified. The number of machines that could do textile work is so small that the first time Litowsky and Rinearson watched yarn being produced it was in their own factory.
It took many hours working with electricians and other tradesmen to build and redesign the machines in the factory. Litowsky said he was surprised by the quality of the work done by local workers.
“I can’t say enough about the people who have worked with us,” he said.
The factory employs around 10 people and there are two shifts that operate, the first starting at 4 a.m. when Litowsky arrives. Since production began, the company has made nearly 100,000 high-end shirts. The company has consumed 160 bales of cotton. Yarn is made in the factory from cotton bales grown in nearby fields. Opening an American-owned textile firm and using homegrown cotton was important to the partners.
“It’s why we came here,” Rinearson said.
Litowsky concurred, noting that he understands the frustrations of a group of American workers that have been declining in recent years as manufacturing moved overseas.
“We’ve seemingly forgotten about a large group of people out there,” Litowsky said of those connected to U.S. manufacturing.
Most of their customers are in places such as New York and Miami, but Litowsky said he hopes the company can make in-roads with local garment producers. The yarn is made in the factory, but the cutting and sewing that goes into creating the clothes is done at a facility in Minnesota. At some point, they hope to expand the Jonesboro facility to include the sewing and cutting operations.
Owning a textile manufacturing business is a world different than the one Litowsky grew up in. Litowsky auditioned for an Oreo cookie commercial in 2001 and won the role. No one in his family had any formal acting experience, but soon after he would appear in dozens of commercials. Not long after he was cast as the son in the television show “Hope & Faith,” more television and movie parts ensued. Regis Philbin once said in an interview that Litowsky was like a “40-year-old trapped in the body of a 5-year-old.”
One skill an actor must have is the ability to transition from one role to the next. Hours on sets are long, and actors have to quickly seize on opportunities when they are presented, he added. That work ethic and skill set translates to the business world, he said.
Rinearson also has dealt with his share of obstacles through the years. In his youth, he suffered from a nerve condition that left him hospitalized for several years. The long stretches of isolation helped hone his focus, especially when it came to studying subject areas such as math and science.
When he got to college, Rinearson decided to study physics. In the midst of his college career, Litowsky approached him with the yarn factory idea. At one point, he started taking classes at Arkansas State University so he could complete his degree. A lot of the math and science he’d been exposed to has helped in the business, he said.
The pandemic has hurt retail garment sales during the last year, but Litowsky and Rinearson are hopeful the markets will improve in 2021, and they will be able to expand their customer base. Litowsky would like to expand into child clothing and even some types of sports apparel.
How do they plan to make HPR successful in the coming decade?
“Quality. It’s the one thing we got. The only way we can compete is to offer better quality,” Litowsky said.